Distribution ERP Built
For Your Industry
Features and Deployment For Your Specific Needs
Aptean Distribution ERP has been built from the ground up to solve the challenges of consumer goods importers and distributors. The system streamlines and optimises your entire supply chain with built-in functionality such as embedded EDI, retail compliance management, long lead time forecasting and chargeback management tools. To suit your business even further, our distribution ERP can be deployed either in the cloud or on-premise, with our team on hand to help streamline implementation.
Backed By Experts In Your Corner
Behind our products is a knowledgeable and dedicated team that understands your business and its unique challenges. Our ERP specialists provide reviews and analysis to ensure your business processes are aligned with industry best practices. Plus, we offer flexible support options that let you choose the level and type of support you need to best meet your unique business needs. So you don’t need to rely on third party support—Aptean has you covered.
Conquer Direct-to-Consumer (DTC) Shipping
As the industry adjusts to the rapid shift towards DTC, equipping your teams with the right tools to process high volumes of shipments easily and efficiently will put you ahead of the curve. That’s why Aptean Distribution ERP Shipment Manager supports seamless integrations with all the major carriers (UPS, FedEx, USPS, etc.) and offers integrated shipping rate shopping as well as street address verification.
Remove EDI Worries With Managed Services
Electronic data interchange (EDI) is crucial for efficient communication with your partners, but can require significant management. With EDI Managed Services fully integrated into our distribution ERP system, our team monitors and manages day-to-day EDI processes and transactions (including mapping) to ensure everything is moving smoothly—so you can focus on running your business.
"Aptean Distribution ERP is a user-friendly ERP system with a personal touch for support that actually knows us and understands our business needs and offers solutions to meet those needs."
An ERP Built for Bottom Line Impact—Today and Tomorrow
Whether you supply everyday furniture, everyone’s favorite beauty product or that accessory that goes with everything, it's time to break up with labour-intensive processes. With antiquated systems. With extensive customisation and third-party plugins.
To truly thrive in today’s market you need innovative, fully integrated software that’s built from the ground up for your industry, in order to accelerate your growth instead of holding you back.
That’s where Aptean Distribution ERP comes in. Our system is ready to fulfil your specific requirements, right out of the box. So you can be up and running quickly, gaining day-one benefits and speedy ROI.
Are you ready to start increasing visibility, efficiency and profits in your operation?
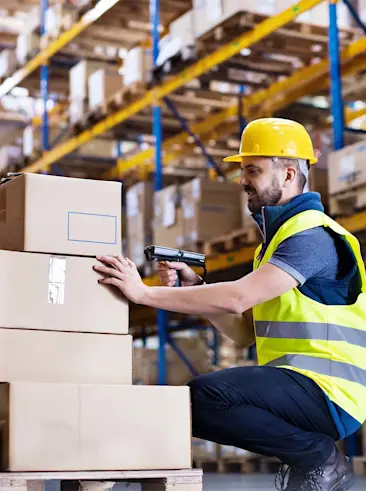
Unlock Distribution-Specific Features and Get the Aptean Advantage
If you’re researching ERP solutions for distribution businesses like yours, you may feel overwhelmed by all the alternatives in the market. Requesting quotes from vendors is one of the ways to find out more about the different options and costs.
You have specialised processes in your distribution business, and you need specialised tools to manage them. If you’re not familiar with distribution ERP platforms, you may have questions about what makes one solution superior to another.
You’re going to need quantitative information to compare them. Start here with this blog post, to find out how requesting quotes fits into the entire process and how best to use it.
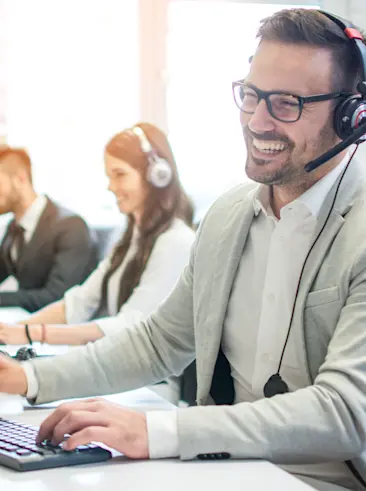
Ready to Serve Your Industry

Home Furnishings
Home Furnishings
We understand the unique business challenges of running a home furnishings business
Whether it is sourcing materials, forecasting inventory and sales, or dealing with retailer compliance issues, our software, Aptean Distribution ERP, is tailored to help home furnishings distributors every step of the way.
ERP for Home Furnishings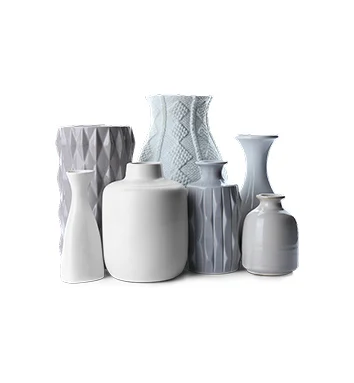
Housewares and Giftware
Housewares and Giftware
We understand the challenges of running your housewares and giftware supply chain
Our Aptean Distribution ERP solution is built for the way housewares and giftware companies run their business. You have unique challenges such as monitoring overseas suppliers, retailer compliance mandates and forecasting for long lead times.
ERP for Housewares and Giftware
Sporting Goods and Toys
Sporting Goods and Toys
From production through retail delivery, we help sporting goods and toy companies improve their entire supply chain
We work with sporting goods and toy companies to simplify complex supply chain requirements, improve bottom lines and increase team productivity integrated all into a single ERP software solution.
ERP for Sporting Goods and Toys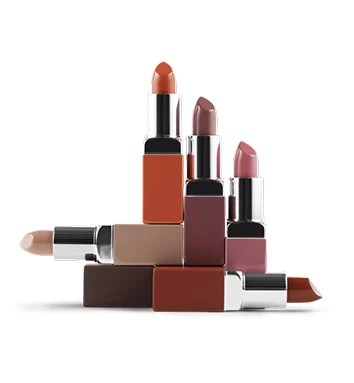
Health and Beauty
Health and Beauty
You face many unique challenges, such as retailer compliance issues, managing long lead times and monitoring production schedules
Aptean Distribution ERP enables health and beauty importers and distributors to improve supply chain visibility, agility and collaboration across their entire supply chain.
ERP for Health and Beauty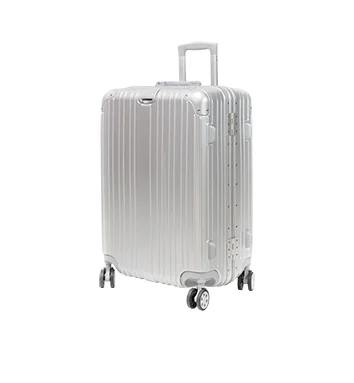
Luggage and Travel
Luggage and Travel
Long lead times, invoice deduction management and retailer compliance mandates are challenges you face in getting products to market
Many luggage and travel accessories companies have general or homegrown ERP software in place that does not provide consumer goods specific functionality to help them compete and win in their industry.
ERP for Luggage and Travel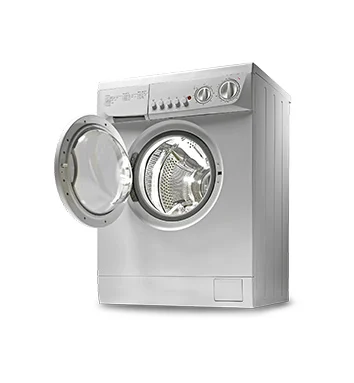
Consumer Electronics and Appliances
Consumer Electronics and Appliances
You face long lead times, retailer compliance issues, tracking high-value products and other unique issues
Aptean Distribution ERP is a fully integrated solution that helps appliance and consumer electronics distributors simplify complex supply chain requirements, improve bottom lines and increase team productivity.
ERP for Consumer Electronics and Appliances
Apparel and Textiles
Apparel and Textiles
You need to have the right tools in place to efficiently run everything from production through retail delivery
We create apparel and textiles specific distribution software that works the way you run your business. Our software is used by thousands of popular brands across the globe to bring their products to customer shelves and consumer hands.
ERP for Apparel and Textiles
Wine and Spirits
Wine and Spirits
Wine and spirits distribution companies have unique wholesale requirements
Our distribution software is built with wine and spirits specific functionality from the start. We know the best way to handle every aspect of your supply chain, including managing bill-backs, compliance and regulatory requirements, and reporting.
ERP for Wine and SpiritsAvailable solutions to drive your digital transformation
Aptean Insights


Ready to start transforming your business?
We’ve got the specialised ERP solutions you need to conquer your industry challenges.
